- As personal protective equipment (PPE) becomes more scarce for hospitals battling COVID-19, some companies offer services to sterilize used gowns and masks.
- Companies, such as privately held San-I-Pak, show sterilizing vital equipment may be a growth area.
- The U.S. has seen the most deaths from COVID-19, topping 22,000. Worldwide, more than 116,000 have died from the disease.
While the scarcity of personal protective equipment (PPE) — masks, gowns, booties — to avert COVID-19 contamination is driving many healthcare workers and public officials to extremes, some sustainable solutions are providing a helpful relief valve.
Enter the autoclave, or sterilizer, and the critical care decontamination system, which together can decontaminate a host of PPE essential to front-line medical personnel treating patients with COVID-19.
One maker of these sterilizers is San-I-Pak Inc., a Tracy, Calif.-based company, which can produce a new machine about every two weeks. Last week, San-I-Pak shipped a sterilizer to the Veterans Administration hospital in the Bronx, New York. San-I-Pak also delivered another autoclave to Bellevue Hospital in New York City in 2018.
“If hospitals, including VA medical centers that have on-site medical waste treatment equipment, start sterilizing certain PPEs right away, they could aid our country through this crisis by lowering the demand for those PPEs,” Darrell Henry, former chairman of the National Energy Resource Organization (NERO), an organization that focuses on energy issues, and the principal of ROQ Strategies, a Washington, D.C.-based PR firm, told Karma.

Cleaning, rather than replacing this vital equipment after only one use, may be a growth area. The U.S. has seen the most deaths from COVID-19, topping 22,000, with more than 10,000 in New York alone. Worldwide, more than 116,000 have died.
The autoclave or sterilizer is essentially an outsize pressure cooker that’s designed to sterilize medical waste. In these days of COVID-19, it is now used to decontaminate some PPE, including surgical masks, gowns and booties made of linen, polycarbonate and polypropylene, although not items made of polyethylene, like Tyvek, and not the coveted N95 respirator masks. Most U.S. hospitals don’t own these machines, which sell for $250,000 or cost between $10,000 and $15,000 a month to rent.
A spokesman for NYU Langone said that the organization has one sterilizer at each of its three main New York City hospitals, but noted that it now has enough PPEs available that it doesn’t need to sterilize used ones in an autoclave. Bellevue Hospital declined to answer Karma’s request about its use. Neither New York State or New York City responded to Karma’s request for comment on whether they are pursuing that avenue to put more PPEs in circulation.
To get more than one use from N95 respirator masks, the Battelle Memorial Institute, known also as Battelle, headquartered in Columbus, Ohio, is leading the charge. According to the U.S. Food and Drug Administration (FDA), the N95 mask reduces wearers’ exposure to particles, including small particle aerosols and large droplets, and are thought to offer healthcare workers the best protection.
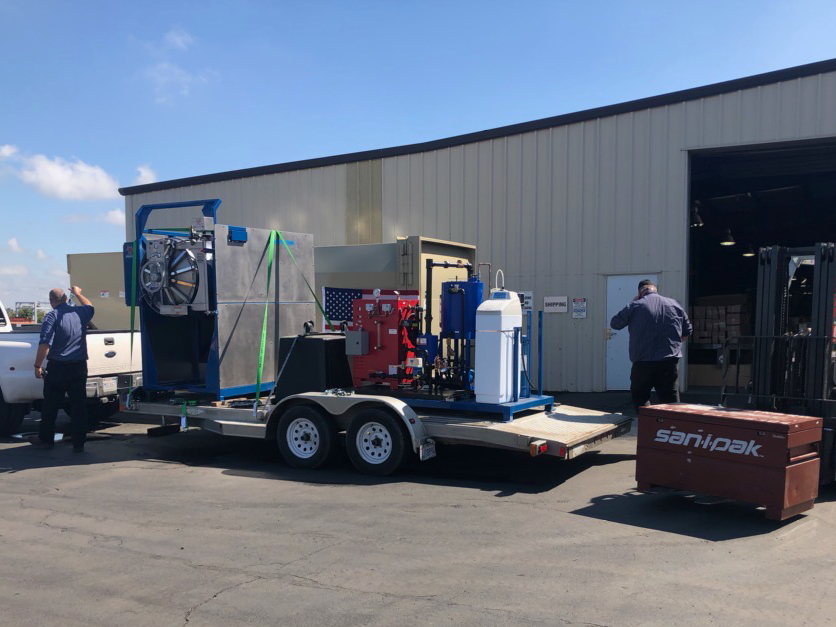
At no cost to hospitals, Battelle can sterilize the masks as long as they are not made of cellulose, using concentrated, vapor phase hydrogen peroxide (VPHP) in a chamber. The machine can handle tens of thousands of masks at once. According to the company, a mask can be decontaminated multiple times without degrading it.
Typically, hospitals and other facilities get a 72-hour turnaround on their orders. Once the masks arrive at a Battelle facility, personnel place a barcode on each and affix the number of times it has been cleaned. The decontaminated masks are returned to the facility that sent them.
The Defense Logistics Agency, under the U.S. Department of Health and Human Services and the Federal Emergency Management Agency, awarded Battelle $400 million to provide N95 decontamination across 60 sites. Facilities are now in central Ohio, Stony Brook, N.Y., and Washington State. Additional sites are planned for Boston, Brooklyn, N.Y., Chicago and the Washington, D.C., area.
Battelle, a nonprofit research institute that also studies agribusiness, ecology and the environment, health, national security and STEM education, opened in 1929.
Photos courtesy of San-I-Pak Inc.